(邦訳:実際のファブリケーション過程を考慮した三次元形状最適化)
![]() |
中島 一崇 東京大学大学院情報理工学系研究科創造情報学専攻 特任助教 |
キーワード
デジタルファブリケーション | 手作業による前処理・後処理 | 形状処理 |
[背景]デジタルファブリケーションが広く一般に普及
[問題]ファブリケーション前後に時間のかかる前処理・後処理が必要
[貢献]形状最適化を通じて前処理・後処理を軽減
デジタルファブリケーション技術は,実際の製造業での利活用が開始されるなど,非常に注目を集めている分野である.また,工学の分野に限らずコンピュータグラフィックス(CG)分野においてもデジタルファブリケーションに関する研究が活発に行われている.このように世間の注目を集め,研究も盛んに行われる分野である一方,デジタルファブリケーションが一般に普及したとは依然として言い難い.デジタルファブリケーションの普及を妨げる大きな理由の1つとして,『手間』が挙げられる.
デジタルファブリケーションの過程は,(1)CADソフトウェアやスカルプトソフトウェアを基に三次元形状を制作する,(2)三次元形状をファブリケーションするための前処理を行う,(3)3Dプリント等を用いてファブリケーションを行う,(4)造形物に対する後処理を行う の4つの工程に分けられる.この中でも特に,前処理や後処理の大半は手作業で行われており,デジタルファブリケーションを行うアーティストや3Dエンジニアにとって大きな負担となってしまっている.更に前処理・後処理の具体的な作業内容はファブリケーション技術に大きく依存しているため,手間の種類も大きく異なる(例:熱溶解積層法による3Dプリントの際のサポート構造の追加をはじめ,サポート構造の除去や造形物の表面をヤスリで整える処理など).そして,このような前処理や後処理を対象とした研究はあまり行われてこなかった.実際の前処理・後処理にはさまざまなものがあるが,本研究では,具体的な2例として,「型を用いた造形技術」と,「粉末(例:石膏)を利用する造形技術」における前処理・後処理の手間に注目し,それらを軽減するための手法を提案した.
型による造形では,造形物を型から取り外す際に「型に引っかかることなく取り外すことができる」ことが常に保証されていなければならない.一般的には,この制約条件を満たすため,プラモデルのようなパーツへの分割が行われる.一方,このような分割は手作業で行われており,熟練の技術が必要となっている.本研究では,このような分割作業を支援する技術を提案することで,専門家でないユーザでも自由形状を複製するための型形状を容易にデザインすることが可能となった.
3Dプリントでは,材料費を削減するために内部空洞をくり抜く処理が一般的に利用されている.特に,粉末タイプの3Dプリントでは,熱溶解積層法と異なり,インフィルと呼ばれる保持構造が必要とならない.反面,凝固されていない粉末が内部空洞に残留してしまう.このような内部に残留した粉末を除去・再利用するためには三次元形状に粉を排出する穴(排出口)が必要となる.排出口の配置作業は,デザイナや3Dプリントエンジニアが手作業で決定しており,粉の排出性能についてあまり考慮できていないのが現状である.本研究では,対象形状の各部分における「粉の排出性能」を推定し,最適な排出口の位置を自動計算する手法を提案した.
[貢献]形状最適化を通じて前処理・後処理を軽減
デジタルファブリケーション技術は,実際の製造業での利活用が開始されるなど,非常に注目を集めている分野である.また,工学の分野に限らずコンピュータグラフィックス(CG)分野においてもデジタルファブリケーションに関する研究が活発に行われている.このように世間の注目を集め,研究も盛んに行われる分野である一方,デジタルファブリケーションが一般に普及したとは依然として言い難い.デジタルファブリケーションの普及を妨げる大きな理由の1つとして,『手間』が挙げられる.
デジタルファブリケーションの過程は,(1)CADソフトウェアやスカルプトソフトウェアを基に三次元形状を制作する,(2)三次元形状をファブリケーションするための前処理を行う,(3)3Dプリント等を用いてファブリケーションを行う,(4)造形物に対する後処理を行う の4つの工程に分けられる.この中でも特に,前処理や後処理の大半は手作業で行われており,デジタルファブリケーションを行うアーティストや3Dエンジニアにとって大きな負担となってしまっている.更に前処理・後処理の具体的な作業内容はファブリケーション技術に大きく依存しているため,手間の種類も大きく異なる(例:熱溶解積層法による3Dプリントの際のサポート構造の追加をはじめ,サポート構造の除去や造形物の表面をヤスリで整える処理など).そして,このような前処理や後処理を対象とした研究はあまり行われてこなかった.実際の前処理・後処理にはさまざまなものがあるが,本研究では,具体的な2例として,「型を用いた造形技術」と,「粉末(例:石膏)を利用する造形技術」における前処理・後処理の手間に注目し,それらを軽減するための手法を提案した.
型による造形では,造形物を型から取り外す際に「型に引っかかることなく取り外すことができる」ことが常に保証されていなければならない.一般的には,この制約条件を満たすため,プラモデルのようなパーツへの分割が行われる.一方,このような分割は手作業で行われており,熟練の技術が必要となっている.本研究では,このような分割作業を支援する技術を提案することで,専門家でないユーザでも自由形状を複製するための型形状を容易にデザインすることが可能となった.
3Dプリントでは,材料費を削減するために内部空洞をくり抜く処理が一般的に利用されている.特に,粉末タイプの3Dプリントでは,熱溶解積層法と異なり,インフィルと呼ばれる保持構造が必要とならない.反面,凝固されていない粉末が内部空洞に残留してしまう.このような内部に残留した粉末を除去・再利用するためには三次元形状に粉を排出する穴(排出口)が必要となる.排出口の配置作業は,デザイナや3Dプリントエンジニアが手作業で決定しており,粉の排出性能についてあまり考慮できていないのが現状である.本研究では,対象形状の各部分における「粉の排出性能」を推定し,最適な排出口の位置を自動計算する手法を提案した.
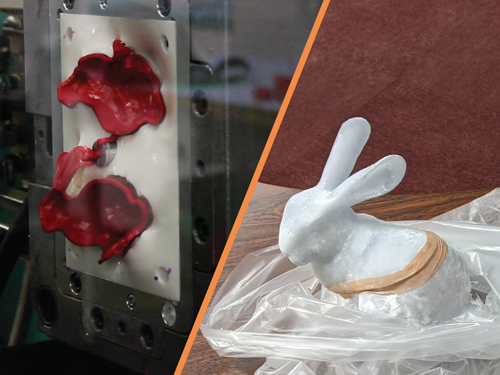
動画URL(YouTubeチャンネル用): http://visualcomputing.ist.ac.at/publications/2018/CoreCavity/ 論文の動画URL:https://www.youtube.com/watch?v=UZ9hR9qLMAY |
(2020年5月29日受付)